Understanding the Impact of Injection Molded Plastics Suppliers on Your Business
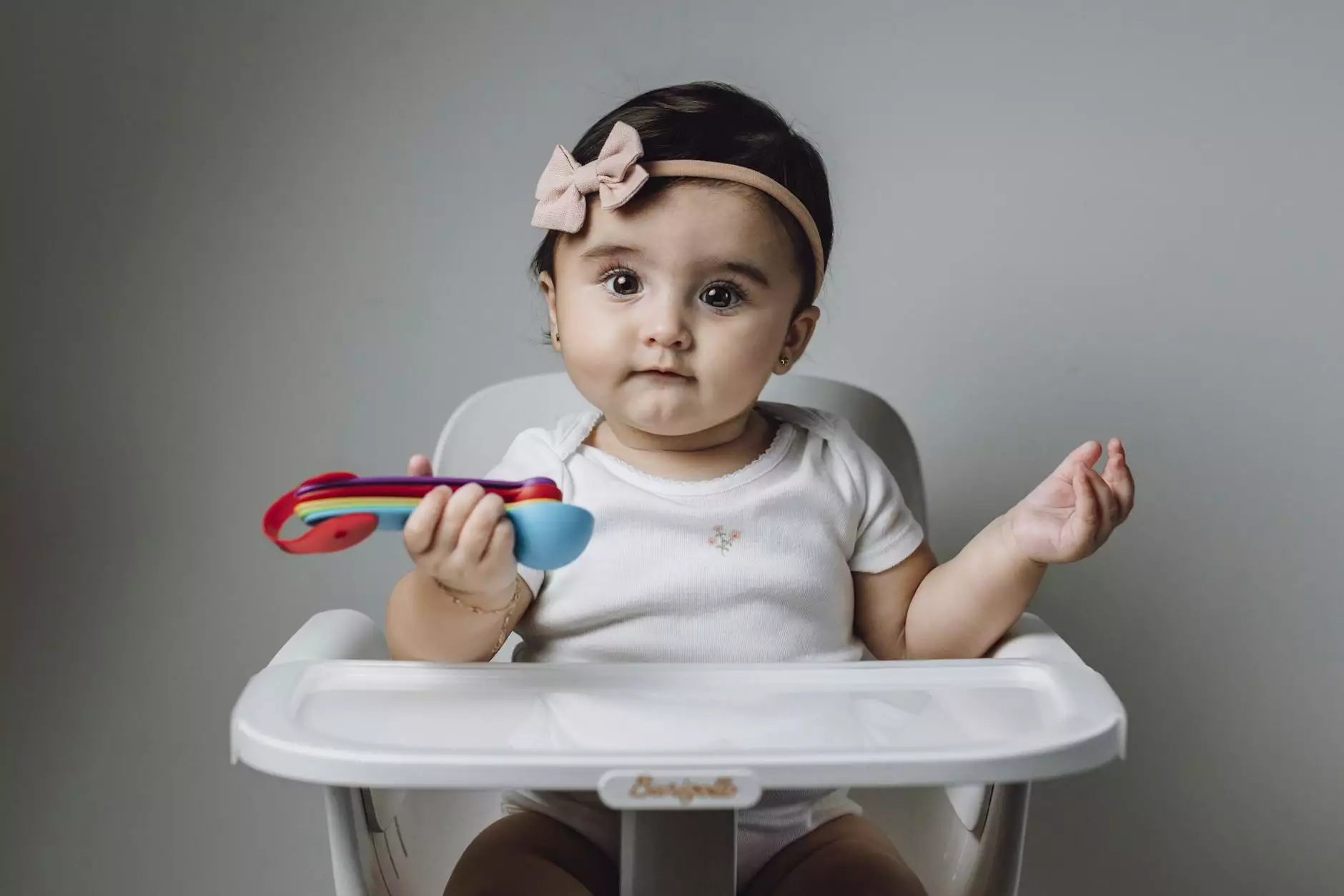
In the ever-evolving landscape of manufacturing, injection molded plastics suppliers play a critical role in various industries. From automotive to consumer goods, the versatility and efficiency of injection molding have made it a cornerstone of modern production. This article explores the comprehensive benefits of collaborating with reputable injection molded plastics suppliers like Deep Mould, ensuring you understand how they can transform your business operations.
The Importance of Injection Molding in Modern Manufacturing
Injection molding is not merely a manufacturing process; it is an innovative technology that allows for the production of complex shapes and designs with incredible precision. This method has revolutionized the way products are developed, bringing several advantages:
- Cost Efficiency: Injection molding reduces waste and optimizes material use, leading to lower production costs over time.
- Design Flexibility: The technology allows for intricate and complex part designs that would be impossible with traditional manufacturing methods.
- High Volume Production: Injection molding is ideal for large-scale production runs, offering consistent quality through automated processes.
- Material Variety: A wide range of plastics can be used, enabling choices that suit specific product needs.
Choosing the Right Injection Molded Plastics Suppliers
When it comes to selecting an injection molded plastics supplier, several factors should guide your decision:
1. Experience and Expertise
The supplier's experience in the industry can significantly impact the quality of the molded parts. Established suppliers often have the knowledge and resources to handle complex projects efficiently.
2. Quality Assurance
Look for suppliers that adhere to strict quality control measures. Certifications such as ISO 9001 can indicate a commitment to quality. High-quality plastics ensure that your products meet industry standards and customer expectations.
3. Customization Capabilities
Each project has unique requirements. A reliable supplier should be able to offer tailored solutions, from material selection to bespoke part design.
4. Technological Advancements
Suppliers who invest in the latest technology can provide improved efficiency, reduced production times, and enhanced product quality.
5. Customer Support
Effective communication and support can greatly influence project success. A dedicated account manager or customer service team can help address concerns and provide updates throughout the manufacturing process.
Key Benefits of Partnering with Top Suppliers
Engaging with prominent injection molded plastics suppliers offers numerous benefits that go beyond mere production capabilities:
1. Innovation and R&D Support
Top suppliers not only produce parts but also collaborate on research and development. They can provide insights that drive innovation and help you stay competitive in your industry.
2. Speed to Market
In today's fast-paced market, time is of the essence. Reliable suppliers streamline the production process, enabling you to bring your products to market faster while maintaining quality.
3. Sustainability Practices
Many leading suppliers emphasize sustainability by adopting eco-friendly materials and processes, which not only benefit the environment but can also enhance your brand reputation.
4. Scalability
As your business grows, your supplier should be able to scale production to meet increasing demand without sacrificing quality.
Injection Molded Plastics: Applications Across Industries
The versatility of injection molded plastics means they find applications in a myriad of sectors:
1. Automotive Industry
Injection molding is crucial for manufacturing parts like dashboards, bumpers, and interior trim. The lightweight nature of molded plastics contributes to fuel efficiency and performance.
2. Consumer Electronics
From casings to intricate internal components, molded plastics are integral in electronics, enhancing aesthetics while providing durability.
3. Medical Devices
High-quality, sterile, and compliant products are essential in healthcare. Injection molded plastics support the production of syringes, housings, and various medical instruments.
4. Packaging Solutions
Injection molding enables the creation of innovative packaging solutions that are not only functional but appealing to consumers.
5. Household Goods
Everyday items, from toys to kitchen tools, benefit from the efficiency and versatility of injection molding processes.
The Future of Injection Molded Plastics
As we look ahead, the future of injection molded plastics is bright, with trends that are shaping the industry:
1. Advancements in Materials
Innovative materials, including bioplastics and recycled resins, are making their way into injection molding, offering sustainable solutions for manufacturers.
2. Smart Manufacturing Technologies
Technologies like IoT and AI are beginning to integrate into the injection molding process, improving efficiency, predictive maintenance, and operational analysis.
3. Increased Automation
The rise of automation in manufacturing will likely drive costs down further while ensuring consistency and quality across production runs.
4. Globalization of Supply Chains
With manufacturers seeking to optimize costs and resources, injection molded plastic suppliers are expanding their reach globally, making it easier for businesses to source parts and materials.
Conclusion: Elevate Your Business with Injection Molded Plastics Suppliers
Partnering with leading injection molded plastics suppliers like Deep Mould can significantly enhance your production capabilities and product offerings. By leveraging the unique advantages of injection molding—cost efficiency, design flexibility, and high-quality output—your business can thrive in competitive markets. As industries evolve, embracing collaboration with proficient suppliers becomes essential for innovation and growth.
Investing in a strategic partnership with a reliable supplier will not only ensure the success of your current projects but also set a solid foundation for future opportunities. Seize the potential of injection molded plastics and transform your business today!