The Power of Plastic Mold Injection in Modern Manufacturing
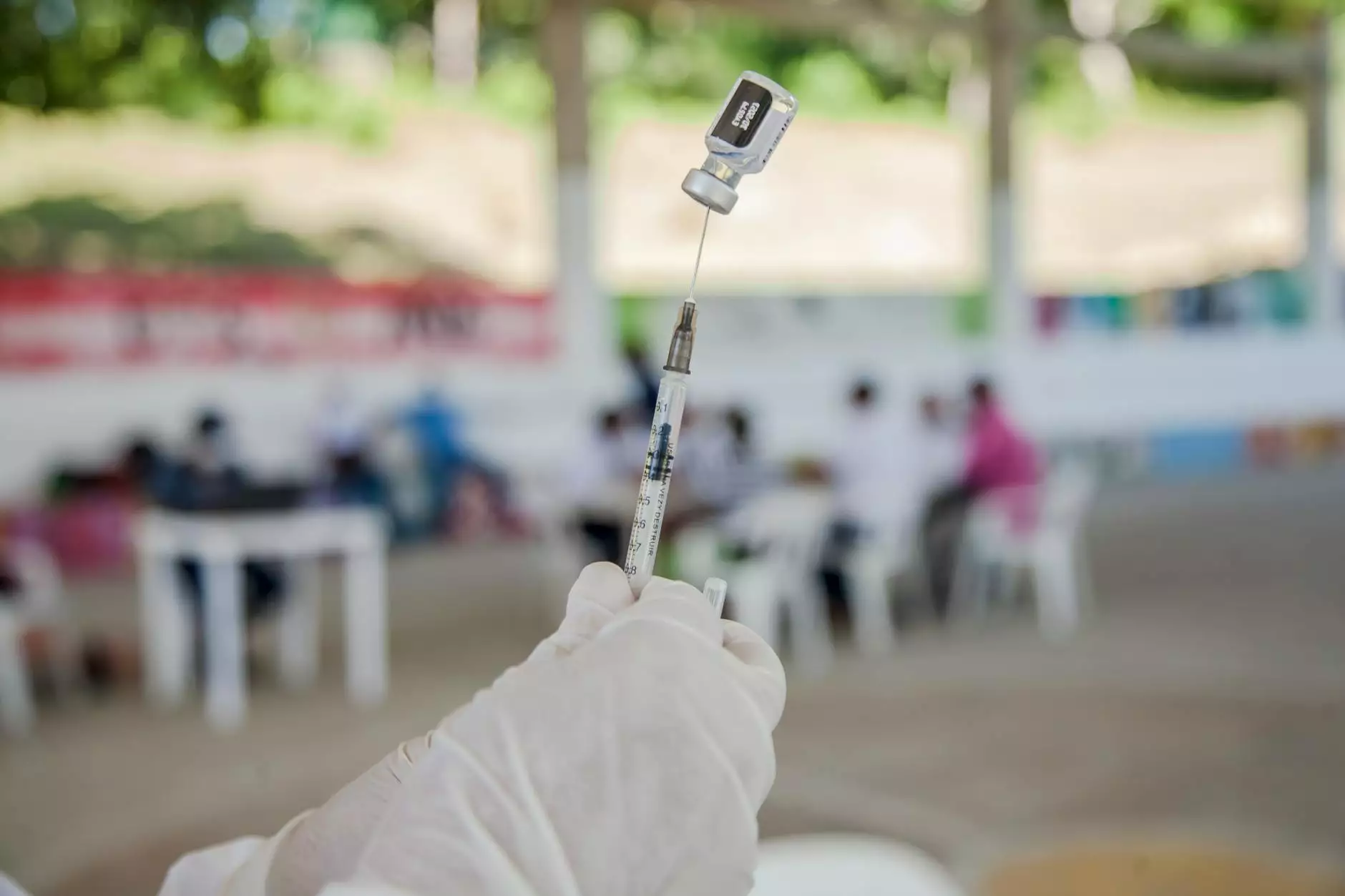
In today's fast-paced industrial world, efficiency and precision are paramount. One of the most revolutionary technologies that have emerged to meet these demands is plastic mold injection. This advanced manufacturing process not only enhances productivity but also significantly improves the quality of products. Businesses focusing on metal fabrication, like Deep Mould, are leveraging this technology to stay competitive and meet consumer demands.
Understanding Plastic Mold Injection
At its core, plastic mold injection is a manufacturing process where molten plastic is injected into a mold to create specific shapes. This process allows for the mass production of detailed and complex parts with remarkable accuracy.
The Process of Plastic Mold Injection
The plastic mold injection process consists of several key steps:
- Design and Mold Creation: Engineers create a digital design of the part, which is then used to construct the mold using durable materials.
- Material Selection: Various types of plastics can be used, depending on the required strength, flexibility, and temperature resistance.
- Melting the Plastic: The selected plastic material is heated and melted until it reaches a viscous state suitable for injection.
- Injection: The molten plastic is injected into the mold under high pressure, filling every cavity to ensure a precise shape.
- Cooling: The injected plastic cools and solidifies in the mold, forming the final product.
- Demolding: Once cooled, the mold is opened, and the finished product is removed.
Advantages of Plastic Mold Injection
The plastic mold injection process offers numerous advantages that make it a preferred method in manufacturing:
- High Efficiency: This process allows for the mass production of parts at a rapid rate, significantly reducing time and labor costs.
- Cost-Effectiveness: Once the mold is created, replicating parts is relatively inexpensive, making it ideal for large-scale production.
- Precision and Consistency: The automated nature of injection molding results in high precision parts with minimal variation.
- Design Flexibility: Complex geometries can be achieved, allowing for innovative designs that can enhance product functionality.
- Material Versatility: A wide range of plastics can be used, each offering different properties suitable for various applications.
Common Applications of Plastic Mold Injection
The versatility of plastic mold injection means it has numerous applications across various industries, including:
1. Automotive Industry
In the automotive sector, plastic mold injection is used to create a variety of components, including dashboards, panels, and even structural parts. The lightweight nature of plastic contributes to better fuel efficiency while maintaining the necessary strength.
2. Consumer Products
Many everyday items, from containers to electronics, are produced using plastic mold injection. This method allows for colorful and intricate designs that meet consumer preferences.
3. Medical Applications
The medical industry heavily relies on plastic mold injection to produce sterile and precise equipment. From surgical instruments to medical devices, this process helps ensure that quality standards are met.
4. Packaging Solutions
The packaging industry has embraced plastic mold injection for creating lightweight and robust containers. This method allows companies to design custom molds that suit their product specifications.
Why Choose Deep Mould for Your Plastic Mold Injection Needs?
When considering plastic mold injection, choosing the right supplier is crucial. Deep Mould is a leading provider in the industry, known for its commitment to quality and excellence.
Expertise and Experience
With years of experience in metal fabrication and plastic injection molding, Deep Mould has developed the expertise necessary to deliver top-quality products that meet the stringent demands of various industries.
State-of-the-Art Technology
Deep Mould invests in the latest technology and equipment to ensure precision and efficiency in every project. This commitment to technology allows them to produce complex parts with unparalleled accuracy.
Customer-Centric Approach
At Deep Mould, clients are prioritized at every step. The team works closely with customers to understand their needs, providing tailored solutions that align with their business goals.
Conclusion
The significance of plastic mold injection in the manufacturing sector cannot be overstated. Its efficiency, precision, and versatility make it an essential process for companies looking to innovate and stay competitive. As businesses like Deep Mould continue to leverage this technology, the future of manufacturing looks bright, promising even greater advancements and developments.
Take the Next Step
If you are considering incorporating plastic mold injection into your manufacturing processes or looking for a reliable partner for metal fabrication, do not hesitate to reach out to Deep Mould. With their expertise, you can elevate your production capabilities and drive your business forward.