Unveiling the Importance of a Lathe Parts Factory in Metal Fabrication
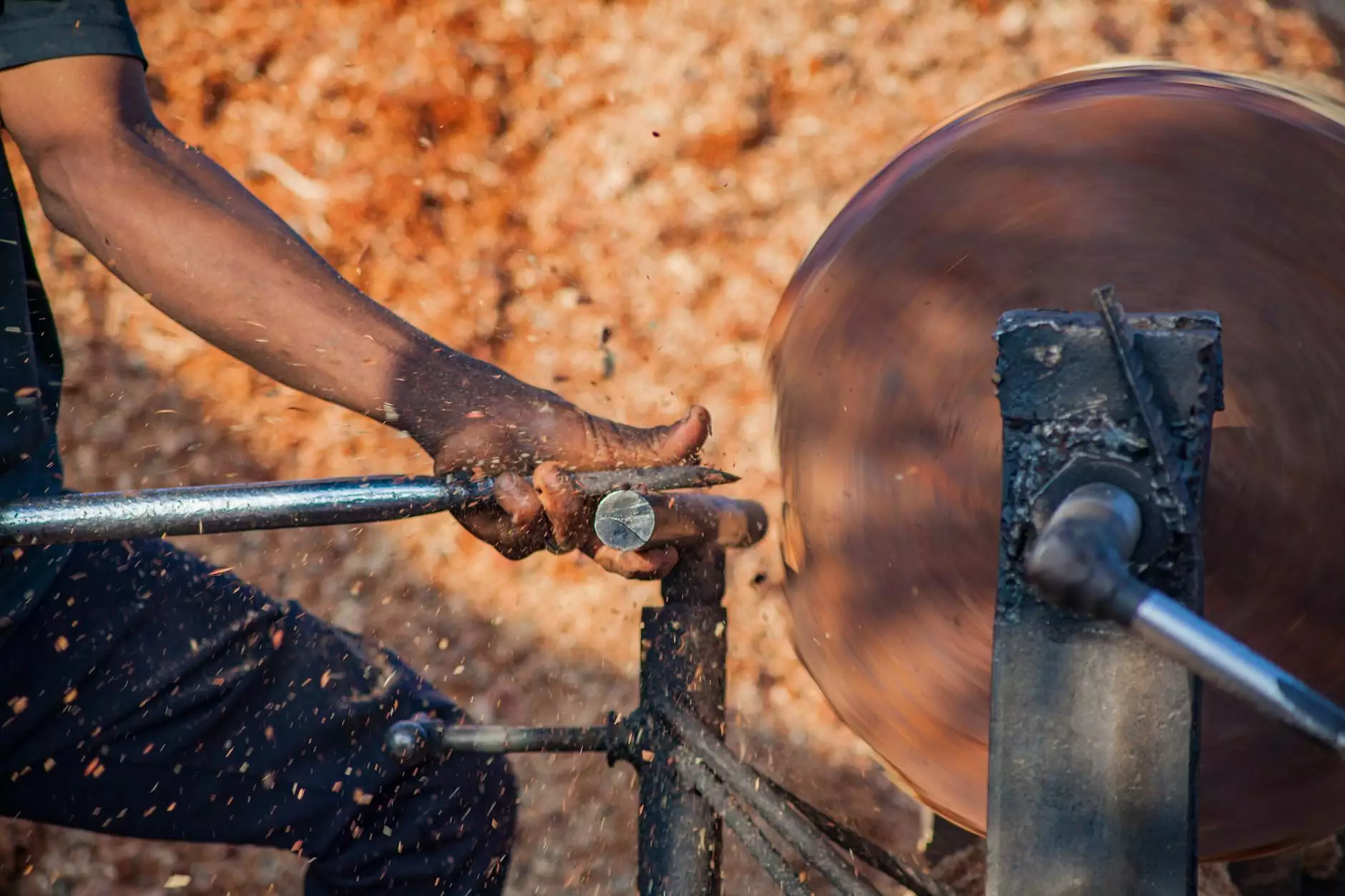
In the realm of metal fabrication, the role of a lathe parts factory cannot be overstated. These specialized facilities are integral to creating precise and durable components used across numerous industries. With advancements in technology and manufacturing processes, understanding the significance of these factories is vital for businesses looking to excel in their fields.
Understanding the Fundamentals of a Lathe Parts Factory
A lathe parts factory is a facility where intricate parts are manufactured using lathes—machines that rotate the workpiece against various cutting tools. This process allows for the creation of a wide array of parts, ranging from simple to highly complex geometries. The components produced often serve as foundational elements in machinery, automotive parts, aerospace applications, and more.
The Manufacturing Process
The process undertaken in a lathe parts factory typically involves several key steps:
- Design and Planning: Each project begins with meticulous planning and design specifications. Engineers must outline the exact dimensions, materials, and tolerances required.
- Material Selection: Choice of materials is critical. Different metals (such as aluminum, steel, or brass) offer varying properties suitable for specific applications.
- Turning Operations: The core of the lathe process involves rotating the workpiece while a cutting tool shapes it. This can include turning, facing, drilling, and boring.
- Precision Measurement: Quality control is paramount. Throughout the manufacturing process, parts must be measured and tested to ensure they meet the precise specifications.
- Finishing Touches: After the turning process, additional finishing operations may take place, such as polishing, coating, or heat treating to enhance durability and performance.
The Impact of a Lathe Parts Factory on Quality Engineering
Quality engineering is at the heart of every successful lathe parts factory. By adhering to stringent standards and employing skilled professionals, these facilities ensure the production of high-quality components. This directly influences the overall reliability and safety of the final products produced by businesses in various sectors.
Benefits of High-Quality Lathe Parts
High-quality lathe parts offer numerous advantages, including:
- Enhanced Durability: Well-crafted components resist wear and tear, leading to longer lifespans and reduced maintenance costs.
- Improved Performance: Precision parts contribute to the smooth operation of machinery, resulting in better efficiency and productivity.
- Cost-Effectiveness: Investing in high-quality parts may have a higher upfront cost but can save money by minimizing repairs and downtime in the long run.
- Customizability: A lathe parts factory can produce bespoke components tailored to the specific needs of businesses, ensuring a perfect fit for unique applications.
Technological Innovations Transforming Lathe Parts Factories
The landscape of manufacturing is continually evolving, and lathe parts factories are no exception. Incorporating cutting-edge technology can significantly enhance the production process.
Automation and CNC Machining
One of the most prominent trends in lathe manufacturing is the adoption of CNC (Computer Numerical Control) machining. This technology allows for high levels of precision and repeatability, which is essential in today’s competitive market.
- Increased Efficiency: CNC lathes can operate continuously, reducing the time required to produce parts significantly.
- Enhanced Precision: Automated processes ensure that tolerances are consistently met throughout the production cycle.
- Reduced Labor Costs: With automation, less manual labor is needed, allowing skilled workers to focus on more complex tasks.
3D Printing and Prototyping
Another revolutionary innovation is 3D printing. While traditionally not associated with lathe parts manufacturing, it is increasingly used for creating prototypes and tooling. This method allows manufacturers to:
- Rapidly Develop Prototypes: Designers can test and iterate on their designs quickly, leading to faster time-to-market.
- Reduce Waste: Additive manufacturing produces less scrap material compared to traditional machining.
The Global Demand for Lathe Parts Factor
As industries grow and evolve, the demand for quality lathe parts produced in factories also rises. Key sectors contributing to this demand include:
Aerospace Industry
The aerospace industry relies heavily on precision components for aircraft and spacecraft. Lathe parts factories play an essential role in creating lightweight yet durable parts crucial for flight safety and performance.
Automotive Sector
With the increasing complexity of automotive designs, the need for high-quality lathe parts has never been greater. From engine components to transmission parts, these factories supply the automotive industry with reliable and efficient solutions.
Industrial Machinery
Industrial machinery manufacturers depend on lathe parts for constructing equipment used in various sectors, such as agriculture, construction, and manufacturing. The durability of these components ensures uptime and productivity in industrial operations.
Challenges Faced by Lathe Parts Factories
Like any sector, lathe parts factories face unique challenges that can affect productivity and quality. Some of these include:
- Skills Shortage: Many experienced machinists are retiring, and there is a growing need for skilled labor to operate advanced machinery.
- Supply Chain Disruptions: Fluctuations in raw material availability and pricing can affect production schedules and costs.
- Competition: With globalization, local manufacturers must compete with overseas factories that may offer lower prices.
The Future of Lathe Parts Factories
The future of lathe parts factories looks promising, driven by advancements in technology, increased demand across multiple industries, and a focus on sustainability.
Embracing Sustainability
As industries worldwide shift towards sustainable practices, lathe parts factories are also exploring eco-friendly methods. This includes:
- Energy Efficiency: Investing in energy-efficient machinery can significantly reduce the carbon footprint of manufacturing processes.
- Material Recycling: Implementing recycling programs helps reuse scrap materials, reducing waste and conserving resources.
Continuous Improvement and Innovation
Successful lathe parts factories will prioritize continuous improvement through adopting new technologies, training workers, and enhancing processes. Staying ahead of trends allows these factories to fulfill the evolving needs of their clients effectively.
Conclusion
In conclusion, a lathe parts factory plays an essential role in the metal fabrication industry, influencing the quality and performance of products across diverse sectors. With continuous advancements in technology and a focus on quality engineering, these factories are equipped to meet the growing demands of the industry. For businesses looking to thrive, partnering with a reliable lathe parts factory, such as those found at deepmould.net, can provide a significant competitive advantage. By understanding the intricacies of manufacturing lathe parts, companies can ensure their products are built to last and perform exceptionally.