Understanding Lathe Machining Parts: A Comprehensive Guide
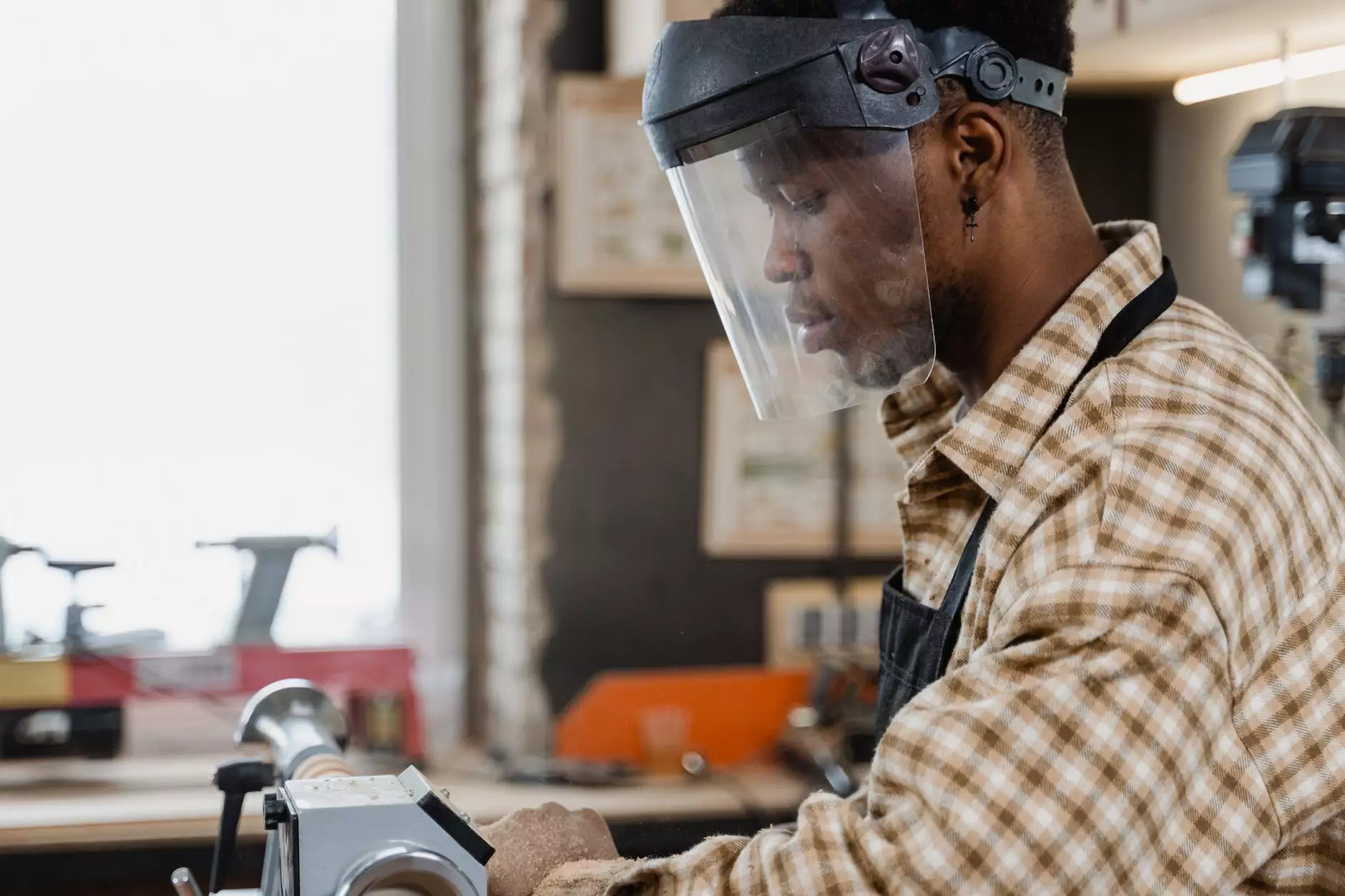
Lathe machining parts represent a crucial element in the world of manufacturing and fabrication. Their significance spans across numerous industries, offering unparalleled precision and efficiency in creating complex components. In this extensive guide, we will explore the nature of lathe machining parts, their applications, benefits, and how businesses can harness their advantages.
1. What are Lathe Machining Parts?
Lathe machining parts are components created using a lathe, a versatile machine tool designed to rotate a workpiece against cutting tools. Through this rotation, various materials can be formed into different shapes and sizes, making lathe machining a cornerstone of production in many manufacturing processes.
1.1 The Lathe Machining Process
The machining process involves several stages:
- Setup: The workpiece is securely mounted on the lathe.
- Turning: The rotating tool removes material from the workpiece.
- Finishing: Additional finishing processes improve surface quality and precision.
This straightforward yet effective method allows machinists to produce incredibly detailed parts that meet specific industry standards.
2. Applications of Lathe Machining Parts
Lathe machining parts serve various sectors, showcasing their versatility. Some major applications include:
2.1 Automotive Industry
In the automotive sector, lathe machining parts produce components such as:
- Engine components
- Transmission housings
- Custom fittings and brackets
These parts require high precision and durability, crucial for vehicle performance and safety.
2.2 Aerospace Sector
The aerospace industry demands unparalleled accuracy. Lathe machined parts are used in:
- Aircraft structural components
- Engine parts
- Fuel system components
The reliability of these parts ensures safety and efficiency in flight.
2.3 Medical Equipment Manufacturing
In the medical field, lathe machining is key for producing parts such as:
- Surgical instruments
- Implants
- Precision medical devices
These components often require strict adherence to regulatory standards, reinforcing the need for high precision.
3. Benefits of Lathe Machining Parts
Investing in lathe machining parts offers numerous advantages:
3.1 Precision
Lathe machining produces highly accurate components with tight tolerances. The precision of the machining process ensures that each part fits seamlessly into its intended assembly.
3.2 Cost-Effectiveness
In bulk production, lathe machining can significantly reduce costs per unit. The efficiency of the process and the ability to produce complex geometries with minimal material waste makes it an attractive option for manufacturers.
3.3 Versatility
Lathe machines can accommodate various materials, including metals, plastics, and composites. This versatility allows businesses to handle a wide range of applications, from small-scale projects to large industrial demands.
4. Key Considerations When Choosing Lathe Machining Parts
To maximize the benefits of lathe machining parts, several factors should be taken into account:
4.1 Material Selection
Choosing the right material is crucial, as it impacts the part’s performance, durability, and cost. Common materials used in lathe machining include:
- Aluminum
- Steel
- Brass
4.2 Tolerances
Understanding the required tolerances for your components is vital. Working with specifications that outline the necessary tolerances will ensure the finished parts meet their performance criteria.
4.3 Surface Finish Requirements
The surface finish of lathe-machined parts can affect performance and aesthetics. Evaluate the necessary finish to ensure functionality, especially in medical and aerospace applications.
5. Quality Assurance in Lathe Machining
To maintain the high standards of lathe machining parts, quality assurance practices must be integrated into production:
5.1 Inspection Processes
Regular inspection of components during and after machining ensures adherence to specifications. Techniques like:
- Dimensional inspection
- Surface finish evaluation
- Nondestructive testing
5.2 Certification Standards
Adhering to industry standards such as ISO 9001 can enhance customer confidence and marketability of lathe machined products.
6. Innovations in Lathe Machining Technology
As technology evolves, so does lathe machining. Key innovations include:
6.1 CNC Machining
Computer Numerical Control (CNC) technology has revolutionized lathe machining, offering greater precision, repeatability, and flexibility in manufacturing. CNC lathes can produce complex parts with minimal human intervention.
6.2 Advanced Materials
The development of new materials, such as composite and lightweight alloys, is shaping the future of lathe machining. These materials often have unique properties, allowing for innovations in design and functionality.
7. Why Choose Deepmould.net for Lathe Machining Parts?
At Deepmould.net, we specialize in providing high-quality lathe machining parts tailored to meet your specific needs. Here’s why you should choose us:
- Expertise: Our team of seasoned professionals brings years of experience in precision machining.
- Quality Assurance: We maintain strict quality control measures to ensure that every part meets the highest standards.
- Custom Solutions: We offer bespoke machining solutions, catering to unique specifications across various industries.
- Timely Delivery: Our efficient production processes guarantee timely delivery, meeting your deadlines without compromising quality.
8. Conclusion
In conclusion, lathe machining parts are essential components across various industries, playing a critical role in manufacturing high-precision products. By understanding the processes, applications, and innovations in lathe machining, businesses can leverage these advantages for their operational needs.
Whether you are in the automotive, aerospace, or medical field, choosing the right supplier for lathe machining parts is crucial. Trust Deepmould.net to deliver quality, precision, and customized solutions that propel your business forward.
Explore your options today, and elevate your manufacturing capabilities with the best in lathe machining.